Audi’s MaterialLoop project to reuse materials from end-of-life vehicles in the production of new cars.
- MaterialLoop project tests the circular economy potential of end-of-life vehicles.
- Audi is building knowledge to close the loop on materials such as steel, aluminum, plastic, and glass.
- Markus Duesmann: “It is our goal to reuse as many materials as possible at high quality.”
- First project successes: recycled steel to be used in up to 15,000 inner door parts for the Audi A4
With its joint project ”MaterialLoop”, Audi is taking the next step toward closing more material cycles in the automotive industry. Together with 15 partners from the research, recycling, and supplier sectors, the brand with the four rings is looking into the reuse of so-called post-consumer materials, which are taken from customer vehicles at the end of their lifecycle, from the automotive sector for the production of new cars. As part of Audi’s circular economy strategy, the project provides valuable insight into how a circular economy can be put into practice.
Up to now, very few of the materials used in the production of new vehicles are recovered from old cars. Steel, for example, usually ends up as structural steel after end-of-life vehicle recycling. Audi wants to change that by reusing secondary materials taken from end-of-life vehicles in the production of new cars. Downcycling, which is a loss of quality in materials resulting from the recycling process, is to be avoided.
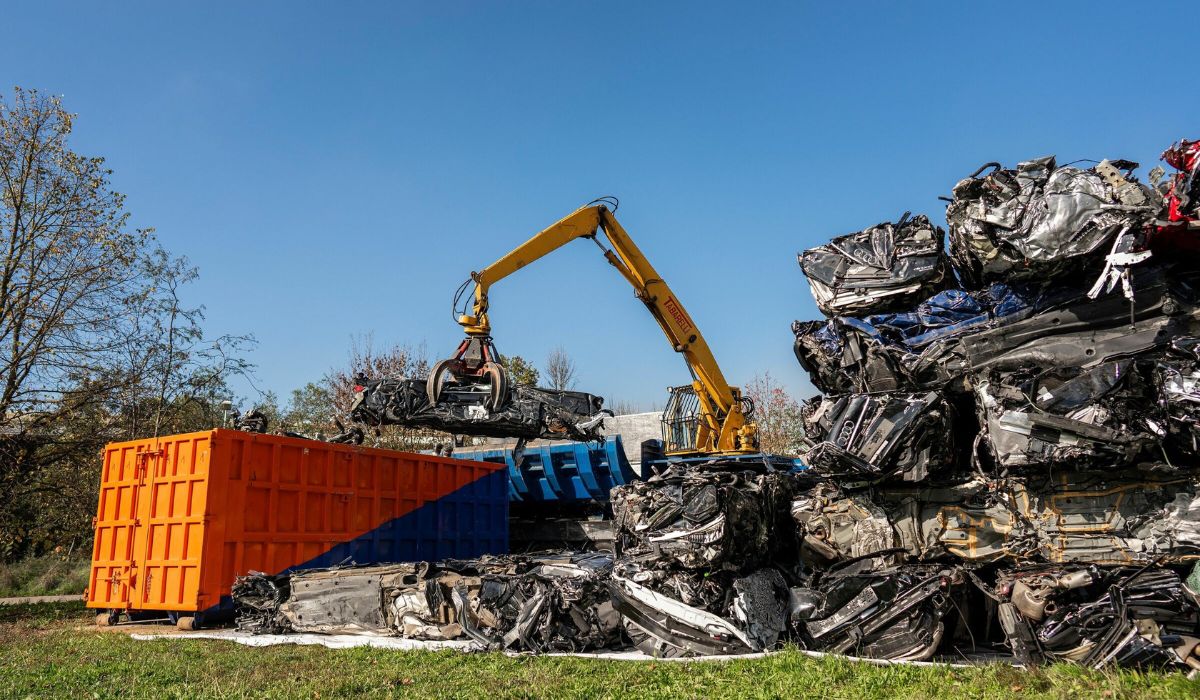
“The MaterialLoop project underscores our ambitious vision to operate a highly efficient circular economy concept for end-of-life vehicles,”
says Audi CEO Markus Duesmann
“It is our goal to recover as many materials as possible at a high level of quality and reuse them in production. This will save valuable primary materials and lower the products’ ecological footprint. Simultaneously, direct access to secondary materials can contribute to increased security of supply. Raw materials would no longer have to be extracted.”
Back in October 2022, 100 vehicles, including among others former development cars, were dismantled as part of the joint MaterialLoop project. The targeted disassembly of individual components alone enabled the retention of high-quality secondary materials such as larger plastic pieces for recycling. After disassembly, the remaining car bodies were shredded and sorted into material groups comprising steel, aluminum, plastic, and glass, in cooperation with the partner companies. With the aim of testing the reuse of such materials in the production of new cars, Audi defined and piloted the further recycling process together with project partners from the recycling industry, the Audi supply chain, and academia.
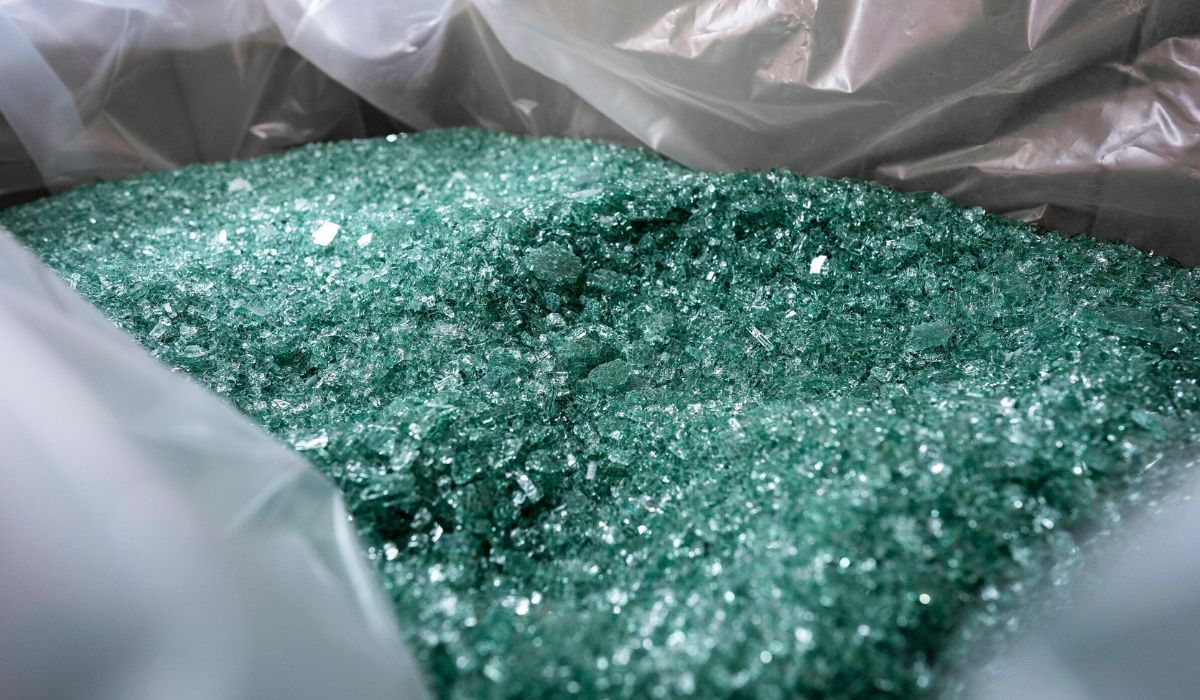
“Our emphasis on cycles within the industry enables us to use our products and the materials they’re made from for as long as possible. Our vision is to rely less on secondary materials from other industries in the future”, explains Johanna Klewitz, head of supply chain sustainability at Audi. Besides the technical feasibility of returning materials in the Audi supply chain, improving future generations of Audi vehicles’ ability to be recycled is also in focus. The project is part of Audi’s circular economy strategy and delivers valuable insights into implementing a circular economy in practice. Dennis Meinen, expert for circular economy at Audi: “At its core, circular economy is about handling resources responsibly. Longevity, repairability, and, indeed, our products’ ability to be recycled are thus all in focus.”
A new life for recycled steel in Audi A4 production
The pilot project will run until the end of April. Despite this, Audi has already been able to put valuable findings from the MaterialLoop project into practice, with some materials now being fed back into automobile production. One result is that much of the scrap steel recycled in the project can be used to make new models. In an initial trial, six steel coils, made from about 12 percent secondary MaterialLoop materials, were produced that match Audi’s high standards for quality and can be used for the most demanding structural components. Audi plans to use the coils to produce up to 15,000 inner door parts for the Audi A4 at the Ingolstadt press plant. Moreover, research undertaken as part of the project, the portion of recycled steel from vehicles in the coil can actually be increased further.
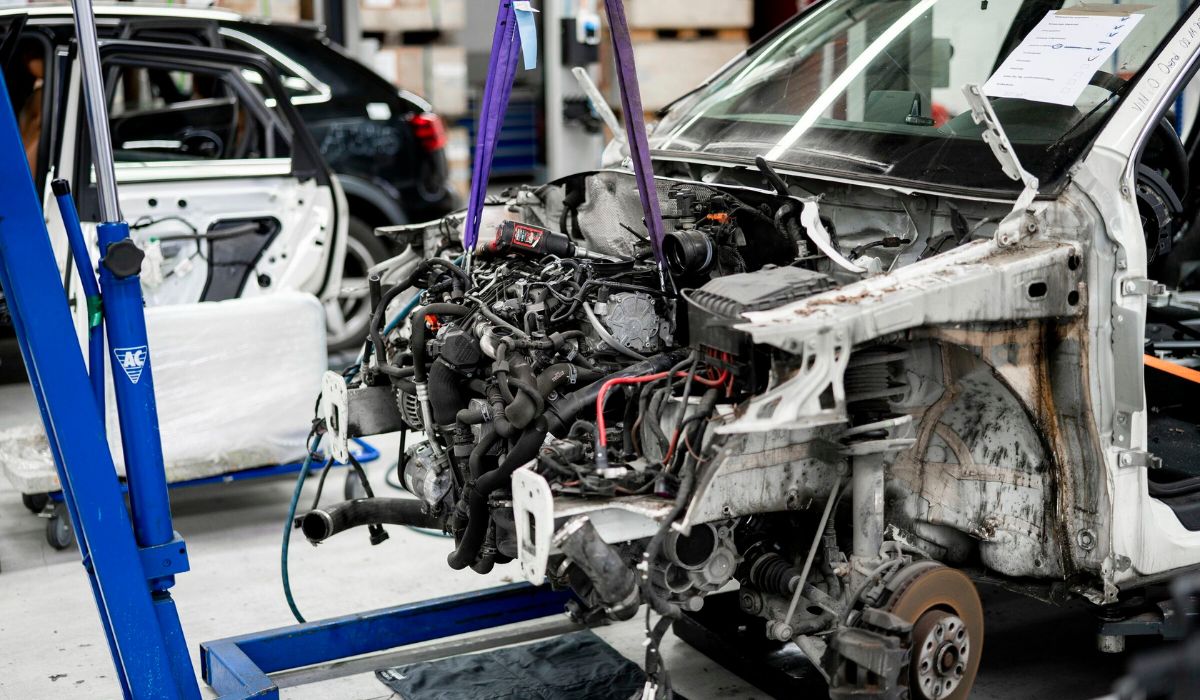
Moreover, together with the project partners, the brand with the four rings is gaining valuable information for the design and construction of future models. Besides improvements in sorting technology, “design for circularity” plays a decisive role in Audi’s efforts to optimize the recyclability of new generations of cars. This means that, as far as the material selection, composition, and modularity are concerned, automotive parts and their components are to be designed in such a way that they can be sorted by material type during end-of-life recycling. As an additional result of the pilot project MaterialLoop, Audi has, working with the Volkswagen Group, developed a guide for suppliers that explains with which premises plastic parts can be designed in a way that further increases the rate of recycling in automotive production.
Experience in glass, plastic, and aluminum recycling
Audi wants to steadily increase the share of recyclates in the Audi fleet over the coming years. Audi Procurement is pursuing the goal of establishing material cycles for automotive applications wherever it is technically possible and makes economic and ecological sense.
To this end, Audi began gathering knowledge on the recycling of used automotive glass in the spring of 2022. In another pilot project. Car windows that are beyond repair are first broken up into small pieces and then sorted. The resulting glass granulate is melted down and turned into new plate glass for the automotive industry – in fact, it is already used in the production of the Q4 e-tron.
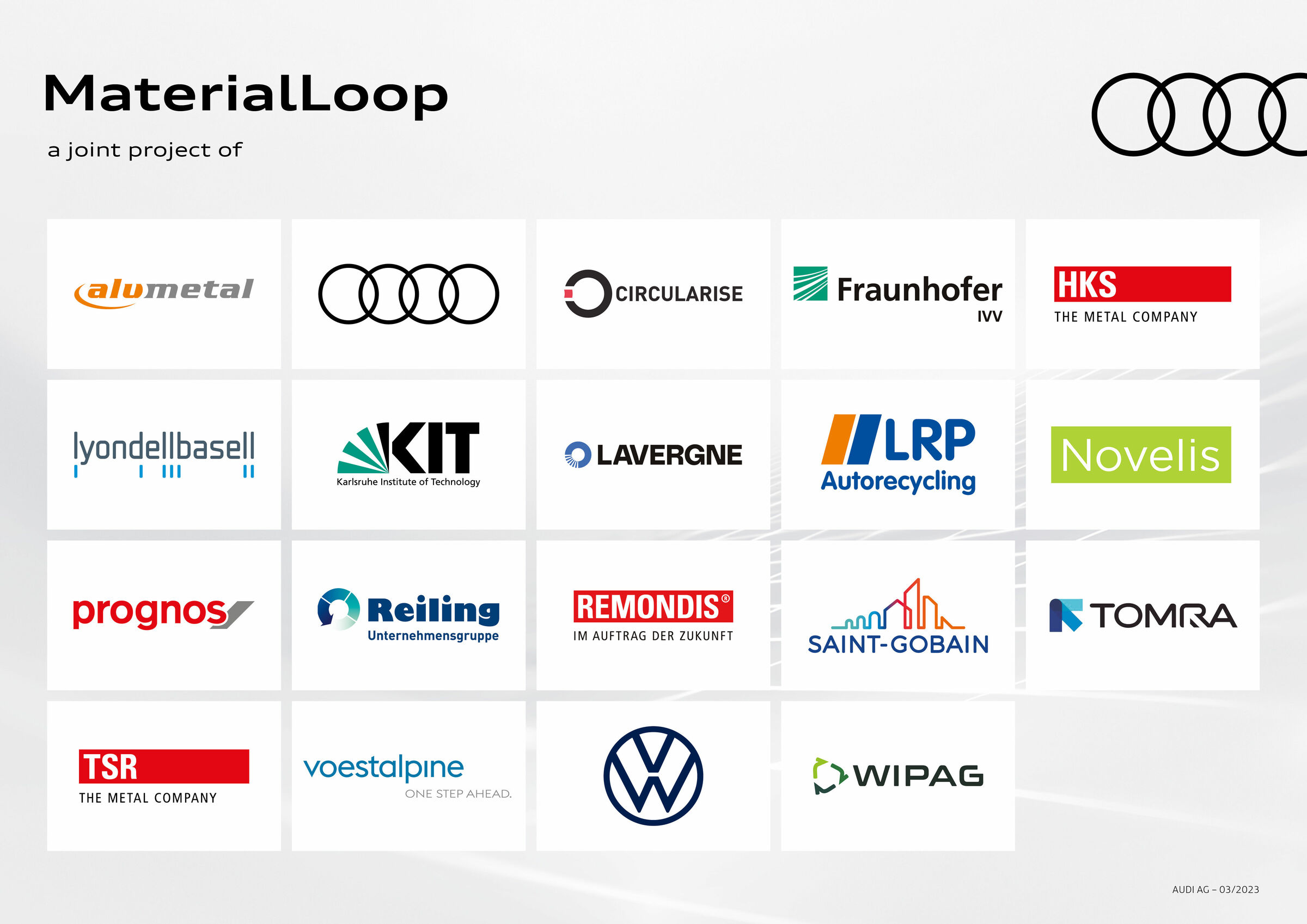
In addition, the brand with the four rings is also deeply involved in plastics recycling. Thanks to PlasticLoop, one of the brand’s three plastics recycling projects, Audi and plastics manufacturer LyondellBasell have established a process that employs chemical recycling for the first time to reuse mixed automotive plastic waste for the series production of the Audi Q8 e-tron. Since 2017, the resource aluminum is managed within a recycling circle at the Audi sites Ingolstadt, Neckarsulm, and Győr as well as at the Volkswagen site Bratislava. Aluminum offcuts that occur during production are returned directly to the supplier. There, they are recycled to form aluminum sheets of the same quality which Audi then reuses in production. This saves precious primary raw materials and ensures the cars enter the use phase with a better environmental balance.